Production at WSS means ...
... Added value with modern technology
WSS places high demands on product quality. The necessary scope for influence is provided by production on an area of almost 20,000 m² and with a high vertical range of manufacture, modern and extensive mechanical equipment and a team that is committed to this quality standard and a permanent improvement process. All relevant metalworking processes are mapped in the value chain. In an industrial environment of specialized suppliers of individual process steps, regular comparisons provide good benchmarks for internal further developments and investments in machinery.
A consistent production layout designed with quality and efficiency in mind enables a transparent, unidirectional production flow and simple internal logistics. The diversity of the product range and a high variance of batch sizes in production and in the different production steps are reflected in the amount of information that is processed for production control with a modern ERP system.
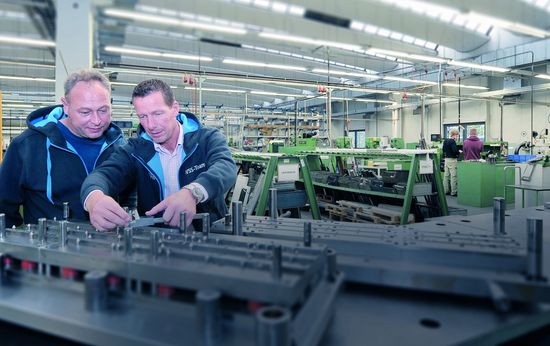
Experienced employees at WSS
Experienced employees who have been with the company for a long time contribute their knowledge and skills to the fulfillment of the tasks and the demands placed on the products.
Employee training and team development pursue the goal of high operational flexibility and personal responsibility at every point in the process.
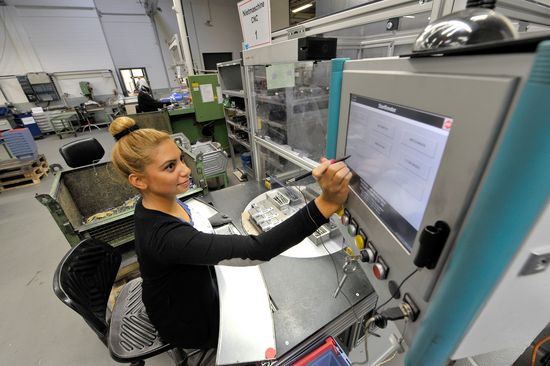
With in-house toolmaking and a team for tool design, capacities and structures are available with which the tool-based forming technology, for which a large number of presses with a pressing force of up to 300 kN are used, can be utilized independently of external resources and expertise and the possibilities for new products and improvements can be continuously exploited. The same applies to the design and manufacture of specific devices that are used in the various five-axis machining centers of the latest design for machining preliminary products.
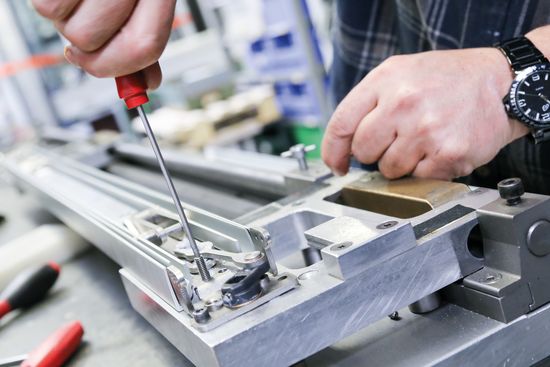
Tool-based forming technology
The tool-bound forming technology and machining are supplemented by several combined laser cutting and punching machines, which together with various special machines, robot-assisted welding workstations and surface treatment equipment form the prefabrication within the company’s production.
Experienced assembly staff combine the products from this prefabrication with purchased components, which have to meet different machine or process requirements, to create WSS products and check their function and compliance with specifications. The assembly workstations are set up according to standards developed within the company that meet the requirements for ergonomics, productivity and flexibility in equal measure.
The logistics center, the heart of which is a modern, fully automated high-bay warehouse with system-integrated picking workstations, marks the end of production and the transition to product delivery. Customer orders and warehouse orders are processed and tracked with system support within the order picking process.